Here at unspun, we don't make clothes - we build tech. From our headquarters in Oakland, California, we're pioneering a technology that will change how the world thinks about and produces apparel.
Our Secret Weapon: The 3D Robotic Loom
At the heart of our innovation is our patented 3D weaving tech, named Vega™. It's so cutting-edge that we have to keep the machine's guts under wraps (or risk getting in trouble with our IP lawyers).
You might have noticed it was blurred out in this recent video from Freethink Media's Hard Reset series (worth a watch if you're curious about our tech).
Traditional weaving vs. 3D weaving: A game-changing difference
To grasp the innovative nature of our technology, it's essential to understand how it differs from traditional weaving.
In conventional 2 dimensional weaving, two sets of yarns (the warp and the weft) are interlaced at right angles to create a flat fabric. This fabric is cut, and the pieces are sewn together to create 3D garments, often resulting in leftover material waste.
Our 3D weaving process, on the other hand, constructs the bulk of the garment as a single, seamless piece. Instead of creating flat fabric that needs to be cut and sewn, our 3D loom weaves the yarns into three-dimensional, circular shapes that can create different sizes and shapes in 3 dimensions. This manufacturing method minimizes waste and allows for unprecedented customization and fit accuracy.
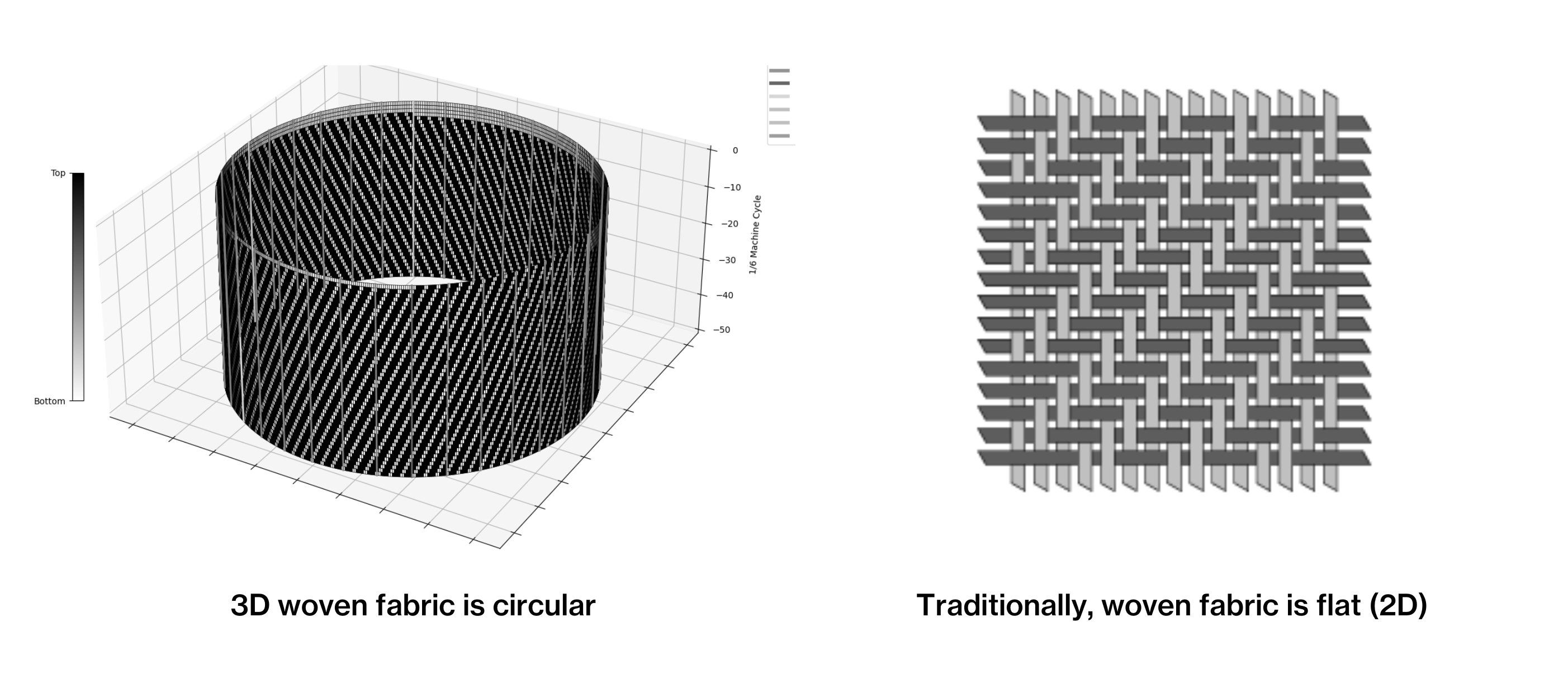
Sustainability is in Our DNA
We're acutely aware of the fashion industry's reputation as one of the world's biggest polluters. That's why we've made sustainability a core part of our mission. Our 3D weaving process builds garments from the directly from yarn, skipping over a bunch of traditional supply chain steps. This means significantly less waste compared to traditional manufacturing methods.
We're not just making clothes - we're working towards a cleaner, more intentional future in the fashion industry.
Read this if you are interested in learning more about how 3D weaving saves resources and reduces waste.
Disrupting Fast Fashion: Beyond Custom-fit
While "fast fashion" has become synonymous with unsustainable practices, we're here to show that speed and sustainability can go hand in hand. Our technology allows for rapid production of garments with minimal waste.
The big idea: If we increase the speed and efficiency of the textile supply chain (by combining multiple production steps) we'll enable brands and manufacturers to produce goods in lower quantities. This also unlocks local for local production, because you go from yarn to garment: all under one roof. A super efficient vertical supply chain.
If apparel companies produce garments closer to where the customers are, they will be able to minimize lead times, optimize their inventory, save money and wasted resources generated from unsold and returned inventory.
If we are to move into an era of sustainable production and consumption, we need to work together to rebuild our connection with the clothing we wear. We think that one way of doing this is by creating clothing made specifically for you; custom-fit and made-to-order.
Even if the price is slightly higher, isn't it better to pay a little more than to purchase a poorly made garment that's so cheap you consider it a throwaway item?
Yet, 3D weaving goes beyond creating custom-fit products for each customer. Even though our machines are capable of creating on-demand and custom-fitted products, it's only part of our solution. We realize that custom-fit is not for everyone (yet), thus our machines can create products in sizes - on-demand or in low quantities. It depends on our partners' preference.
Looking to the Future: hyper-circularity
We are firm believers that circular business models are the future. A future where nothing becomes trash.
Vega™ 3D weaving is prime to aid in this transition. Our process is mechanical. This means our machines can use yarns made from any fiber - they just need to be above a certain tensile strength. We welcome the use of innovative and recycled yarns
What's more, is that we are working on an unwinding technology that will allow us to be fully circular.
Because 3D woven products don't have side seams, the lengths of the yarns are maintained throughout the product's life. This enables us to reuse the yarns without having to mechanically or chemically recycle them. We can just 'unspun' the products back into yarns and use the yarns on the machine again.
Creating new technology is challenging. While achieving full circularity may take us some time, we are unwavering in our commitment to reaching that goal. The first step is to develop beautiful, high-quality, and efficiently made products using our technology. We are building the skyscraper, floor by floor.
As we keep refining our technology, we're dedicated to pushing the boundaries of what's achievable in fashion. We're not just adapting to the future - we're creating it.
If you are still trying to understand, please reach out! We love to talk about our tech.