Here at unspun we’ve been telling the world that 3D weaving will revolutionize the fashion industry. Now we can prove it.
To quantify the environmental impact of Vega™, our 3D weaving platform, we commissioned the fashion supply chain experts at Green Story to conduct a Life Cycle Assessment (LCA) of a 3D woven garment. In short, we wanted to know how much pollution 3D weaving causes compared to the way most clothing is manufactured.
What we found was astounding. Relative to a typical pair of pants that is mass-produced, making a pair of pants with Vega™ reduces greenhouse gas emissions by 53%. It consumes 49% less fuel and electricity. And it requires 39% less fresh water to make in the first place.
The innovations we’re developing today will allow clothing manufacturers and retailers to harm our climate far less, and use far fewer resources, at scale.
Fashion is a wasteful industry. Companies and governments the world over are searching for ways to drastically minimize its global toll. 3D weaving will flip the script.
.jpeg)
What is a Life Cycle Assessment (LCA)?
An LCA is a study of the resources required to make a product, like an article of clothing, and the effect that using those resources to make that product has on the Earth. More directly, an LCA measures the pollution of a product’s supply chain.
The “life cycle” in an LCA refers to the stages of creating a product, from extracting raw materials, to assembling a product’s components, to packaging and selling a finished good. Sometimes this “life cycle” also includes the stages of owning a product until it’s disposed of or recycled. Each of these stages expend measurable quantities of resources, like water to grow cotton, fuel to transport yarn, and electricity to weave it. An “assessment” of these quantities gauges the total impact that each stage has on the environment, and reveals ways to reduce that impact.
Conducting an LCA requires formulating specific questions about a product’s “life” and determining ways to answer them. For Vega™, we sought to learn the extent to which creating a pair of 3D woven pants contributes to climate change, demands energy, and depletes water, according to ISO standards. To better comprehend their significance, our LCA measures these effects against those of creating a typical pair of pants, cut and sewn from an air jet woven roll of fabric. Both products are considered from cradle to gate, that is, up to the point of sale.
Our LCA exists in two parts. Phase 1 examines how we manufacture clothing, and directly compares our Vega™ supply chain to the typical fashion supply chain. Phase 2 examines how much clothing we manufacture and sell, and compares our on-demand business model to the typical inventory business model.
Let’s talk about the details.
How Vega™ performs as a technology
For our purposes, a supply chain describes both the materials and actions that result in an article of clothing. This may seem abstract, but it’s really a story of how you came to wear what you're wearing.
This supply chain begins with converting raw materials into fibers. Our LCA looks at two raw materials, cotton and petroleum. Each requires different manufacturing methods to become yarn, and each leads to a distinct product, a 100% cotton and a 100% polyester pair of pants respectively. Because the former is far more common, we’ll discuss cotton exclusively here.
Both a typical pair of cotton pants and a pair made with Vega™ share one supply chain up to the point of production. Growing and harvesting a cotton crop, ginning and baling cotton, carding and spinning yarn, require the same resources universally. Significantly affecting the impact of these stages is outside of our direct control.
Once yarn has been prepared, however, this one supply chain forks. The stories of each garment abruptly diverge.
Recall that a typical pair of pants is made from patterns. Those patterns are cut from a roll of fabric made with an air jet loom and subsequently stitched together. In contrast, a pair of pants made with Vega™ is 3D woven directly from yarn.
The process of 3D weaving yarn to make clothing has two fundamental benefits, according to our LCA. First, it’s more efficient. Although the operation of a Vega™ 3D weaving machine is more energy intensive than any other stage of our Vega™ supply chain, it uses significantly less electricity than an air jet loom.
Second, it conserves materials. Whereas a Vega™ 3D weaving machine generates 1% fabric loss per pair of cotton pants, conventional manufacturing generates 2.5% loss while air jet weaving a roll of fabric, and 14% during cut and sew assembly.
Combined, these benefits slash pollution output. With a typical pair of pants as a baseline, making a pair of cotton pants with a Vega™ 3D weaving machine reduces greenhouse gas emissions by 24% and consumes 25% less power.
We think these findings show remarkable promise. Through mechanical optimization alone, Vega™ substantially mitigates the impact of every pair of pants at the point of production. Even so, as a technology and a paradigm —as a 3D weaving platform— Vega™ can catalyze even greater environmental savings. It can be its own force multiplier.
.jpeg)
How Vega™ performs as a paradigm
A supply of clothing is something you interact with, whether it’s stacked in sizes on a table, or filtered by size on a website. It’s the story of the way you buy what you’re wearing.
Or at least, it’s the story up till now.
In the typical fashion supply chain, a pair of pants is merely one unit in a large order quantity. The company selling that pair determined the number of pants to mass-produce through demand forecasting before it brought them to market. This created an inventory that the company distributed to stores and warehouses. When you’re ready to purchase a single pair, it has already existed for weeks or months.
The downside of this business model is that the inventory often exceeds demand; a company produces too many pairs of pants. According to our LCA, global fashion brands only sell 70% of the items they make. The remaining 30% is landfilled or incinerated. The cost of consumer convenience is massive waste.
By focusing on a single article of clothing, most LCAs commissioned by fashion brands don’t account for overproduction. Ours, on the other hand, does. This allows for an analysis of the environmental impact that a pair of pants has when it is made in any order quantity.
As a paradigm, Vega™ proposes an on-demand business model. Rather than mass-produce a stock of pants to sell, a company using the Vega™ platform produces pairs of pants after each one is sold. By forgoing inventory, this model ensures that a company sells 100% of the pants they make. When you’re ready to purchase a pair of pants, it is manufactured with a Vega™ 3D weaving machine just hours later.
Both business models are capable of delivering your pants within days of your purchase. Yet the amount of resources either model needs to function is starkly different.
Creating a typical pair of pants also produces more pants than will actually be sold. Because those excess units still necessitate more raw materials, energy, and water to make, they amplify the overall impact of creating one pair. For this reason, with a typical pair of pants made in a large order quantity as a baseline, making a pair of cotton pants on demand with a Vega™ 3D weaving machine reduces greenhouse gas emissions by 53%, consumes 49% less power, and requires 39% less fresh water.
We think these findings are transformative. Through mechanical and sales optimization, Vega™ cuts the carbon footprint and energy demand of every pair of pants in half, and lessens the water used in its creation by two-fifths. The Vega™ platform is a tipping point. It reinvents the fashion industry as an intentional endeavor.
.jpeg)
How 3D weaving achieves sustainability in fashion
Our LCA demonstrates that the environmental savings afforded by the Vega™ 3D weaving platform are neither limited nor incremental. They’re sweeping and extensive.
By changing how we manufacture clothing, Vega™ will minimize the impact that each garment has by way of streamlining production. And by changing how much clothing we manufacture, Vega™ will remediate the harms of the fashion supply chain on a systemic level by way of meeting demand.
These findings are not rhetorical. We seek to effectuate them now. To prevent runaway global warming and its disastrous consequences, our moment calls for quickly implementing big solutions like Vega™.
That’s why we’re teaming up with a growing number of partners to bring 3D woven clothing to a wider audience. From our premier Vega™ collection with Eckhaus Latta to as yet released designs, we’re bullish that we can operationalize fashion brands’ sustainability goals without compromising on the quality of garments or the timeliness of their fulfillment.
By adopting the Vega™ 3D weaving platform, we can begin to refashion fashion for the 21st century.

How can unspun help?
"Key takeaway: unspun has been developing 3D weaving to localize manufacturing since our founding and can produce and scale to 1M+ units within the next 12 months."
Since 2018, unspun has been building proprietary 3D weaving technology and software to make onshore and nearshore apparel production a reality. Our proven system slashes lead times from weeks to minutes, taking pants from yarn to finished garment in a single, seamless process. This process enables labor production time to reduce from 40 minutes to under 15 minutes. It works because it negates the need for many traditionally time-consuming apparel production steps.
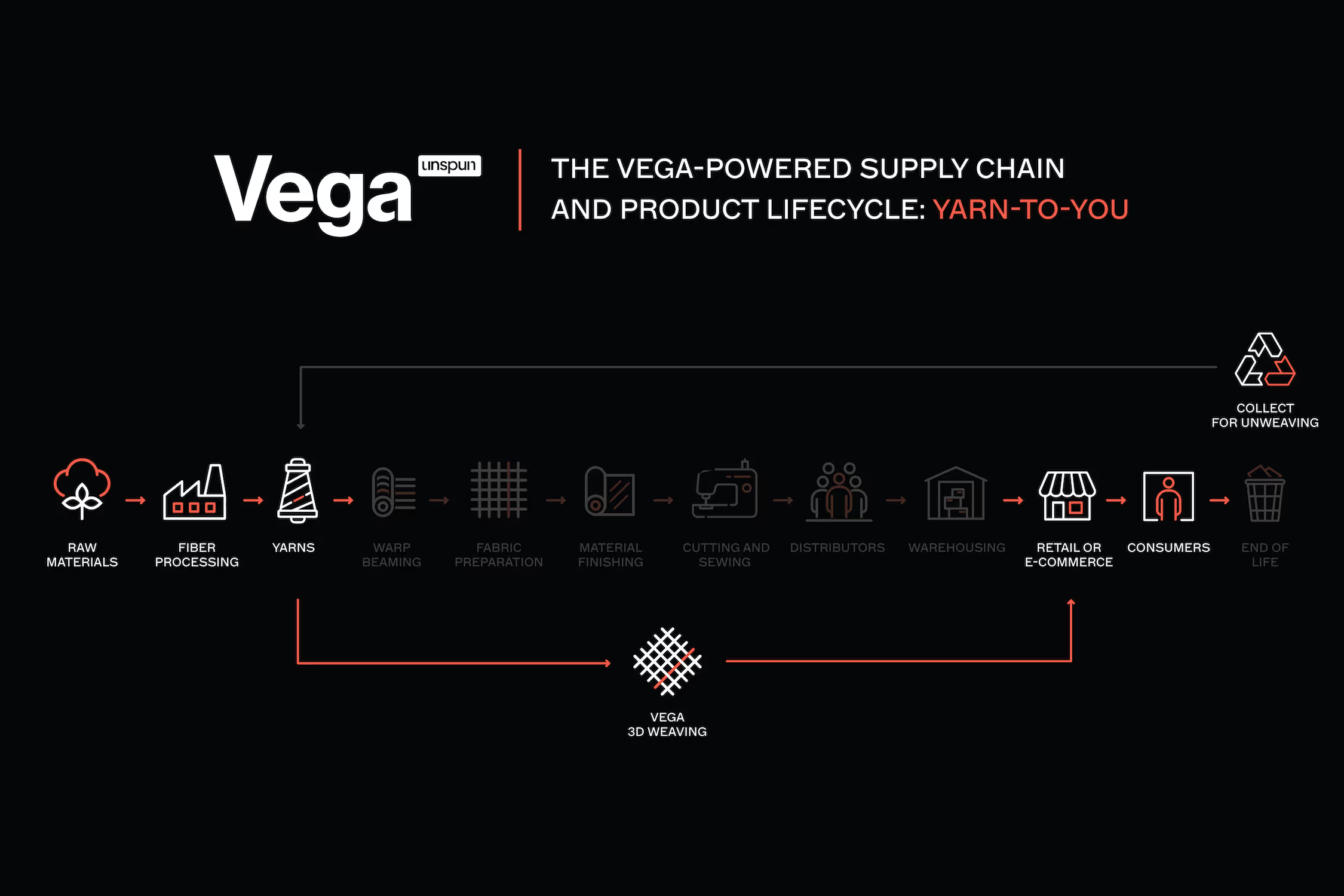
Cost is no longer a barrier: we’re scaling through offtake agreements with major partners like Decathlon and Walmart. We’ve already launched a pilot facility in California and are preparing to open full-scale plants in the US and Europe.
Backed by years of policy work—spanning multiple administrations—we’re on the verge of announcing a US manufacturing consortium alongside leading brands. To power this next phase of growth, we recently closed a $32M funding round, and have committed a significant portion of the funding in helping to onboard brands and manufacturers in the new age of automated apparel manufacturing.
Below is our scheduled capacity:
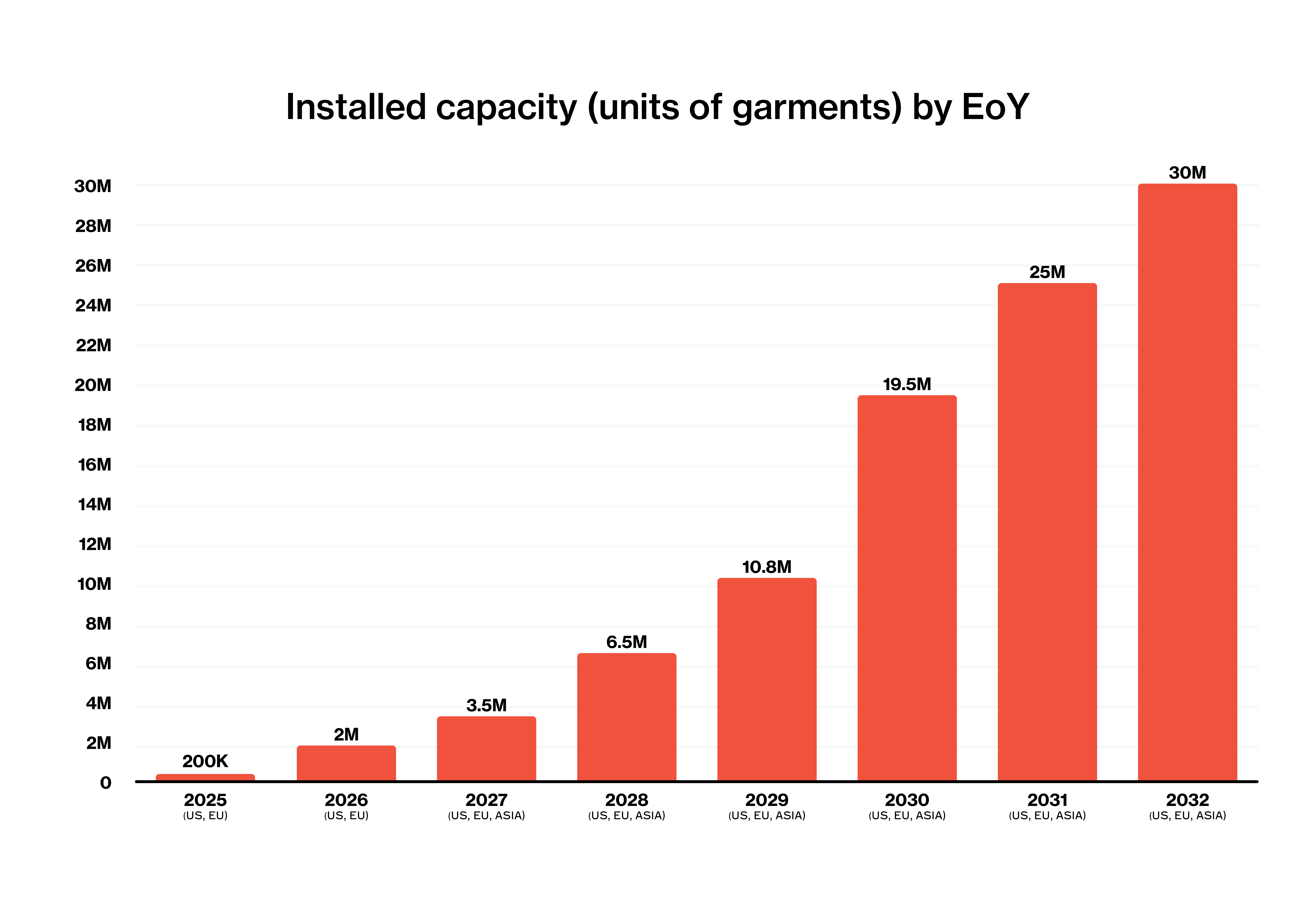
Come see for yourself!
Experience the future of local and automated apparel production with us. We’re hosting exclusive in-person and virtual demonstrations of our 3D weaving technology. Join us!
🇺🇸 San Francisco
Wednesday, April 23, 2025; 5:30-8:30pm
unspun HQ, 6655 Hollis Street, Emeryville, CA
An evening summit hosted by unspun™ and American Circular Textiles. Join us for networking, panel discussions, and hanging out in the world’s first 3D woven powered-microfactory.
RSVP via this registration link.
🇭🇰 Hong Kong
Friday, May 9, 2025, 9:30 - 11:30am
unspun Studio, Shop B2, G/F, 6-10 Shin Hing Street, Central, Hong Kong
An interactive breakfast experience with a live virtual tour of the world's first 3D weaving-powered micro factory and our technology with unspun’s founders
RSVP via this registration link.
🇪🇺 Europe (Coming Soon)
Summer 2025
Secret location
Experience the entire end-to-end process of localized apparel production with 3D weaving in Europe, and be the first to see Vega in action.
Register here to get on the list.
🔗 Can’t make these dates?
Schedule a time to chat or a virtual demo. We’re happy to discuss our pipeline, share machine performance data, or walk you through our upcoming plans.